Литье под давлением
ЛИТЬЕ ПОД ДАВЛЕНИЕМ.
ИНЖЕКЦИОННОЕ ПРЕССОВАНИЕ СИЛИКОНОВЫХ РЕЗИН.
На сегодняшний день важнейшим методом переработки силиконовой резиновой смеси при производстве большого количества изделий и высоких требованиях к стабильности их качества является литье под давлением.
Преимущества метода литья под давлением
Литье под давлением отличается высокой точностью форм. Полная автоматизация процесса гарантирует высокое качество элементов, не требующих дополнительной обработки, и существенное сокращение производственных циклов по сравнению с другими методами. При этом стоимость форм, машин и оборудования выше, чем для других методов. Однако это компенсируетсявысокой производительностью.
Стандартное применение
Метод литья под давлением оптимально подходит для изделий небольших или средних размеров, которые производятся большими партиями, например, соски для детских бутылочек, уплотнительные кольца.
Выбор материала
Для литья под давлением подходит твердая силиконовая резина ELASTOSIL® и жидкая силиконовая резина ELASTOSIL®.
ЛИТЬЕ ПОД ДАВЛЕНИЕМ.
ДОЗИРОВАНИЕ И СМЕШЕНИЕ.
Вязкость этих двух видов резиновых смесей существенно различается, поэтому для жидкой и твердой силиконовых резиновых смесей необходимо разное дозирование и смешение.
Жидкая силиконовая резиновая смесь ELASTOSIL®
Для жидких силиконовых резиновых смесей необходимы специальные дозирующие и смешивающие установки.
Дозирование
Непосредственно из бочонков или бочек насосы дозирующих устройств перекачивают компоненты А и В жидкой силиконовой резиновой смеси в соотношении 1 : 1 в смесительный агрегат, из которого материал затем поступает в цилиндр дозирования литьевой машины. При необходимости добавления пигментной пасты ELASTOSIL® FL она подается в смесительный агрегат по дополнительной линии для подачи пигментов.
Смешение
Смесительный агрегат может быть статическим или динамическим. Статические смесители состоят из неподвижных конструкционных деталей.
Гомогенизация материала происходит в них благодаря неподвижно зафиксированным внутри (способствующим смешению) элементам. Динамические смесители имеют подвижные конструкционные элементы, способствующие гомогенизации материала. Обычно для смешения жидких силиконовых каучуков используются статические смесители. После смешения компонентов А и В материал может под давлением подаваться в форму.
Установка для смешения и дозирования жидкой силиконовой резиновой смеси
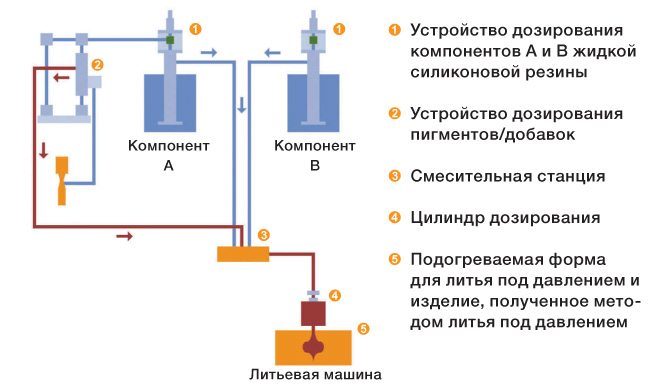
Заполнение формы
Дозирование и заполнение формы смешанным материалом производится при помощи шнека литьевого цилиндра. Современные установки для литья под давлением оснащены очень точными системами управления процессом подачи материала в форму.
Время переработки
При комнатной температуре (ок. 20 °C) смесь компонентов А и В остается пригодной к переработке на протяжении не менее трех дней. При более высокой температуре время пригодности к обработке может соответственно сократиться. Для предотвращения преждевременной вулканизации рекомендуется выполнить термостабилизацию цилиндра дозирования и смесительного агрегата.
Если планируется остановка производственного процесса более, чем на три дня, то литьевой агрегат необходимо промыть, используя один из компонентов.
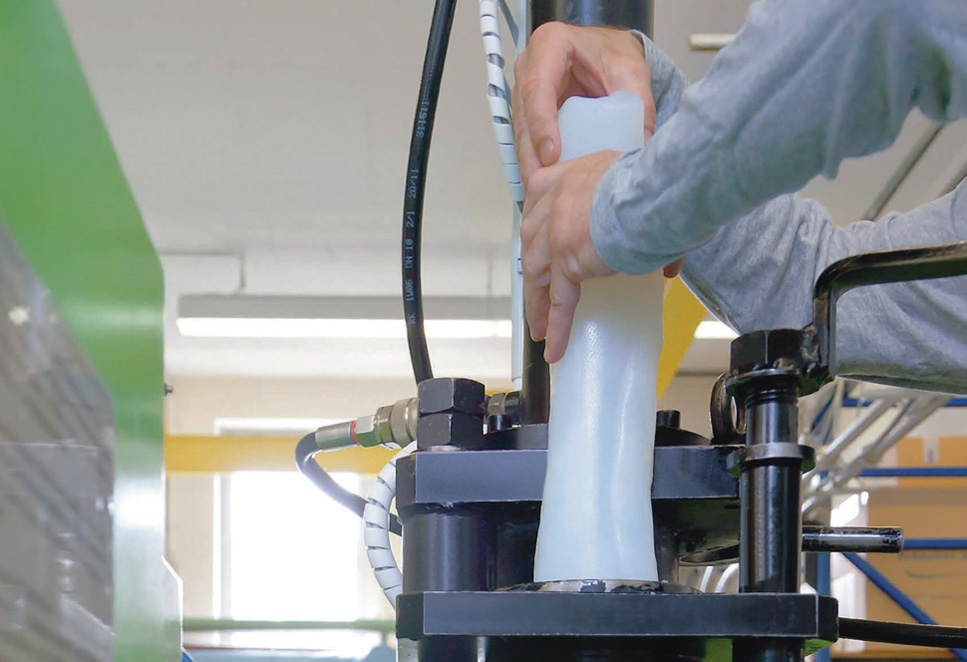
Твердая силиконовая резиновая смесь ELASTOSIL®
Для литья под давлением мы предлагаем два вида твердой силиконовой резиновой смеси ELASTOSIL®:
- различные формы готового к применению материала; преимущественно в виде брусков, но возможно и в форме полос, шнуров круглого сечения и т. п.
- суперконцентрат силиконовой резиновой смеси, к которому добавляется сшивающий агент, а при необходимости - и другие добавки.
- Как правило, смешение производится на специальных вальцах
Дозирование
Стандартная дозированная подача твердой силиконовой резиновой смеси производится при помощи плунжерного устройства литьевой машины. Это процесс полуавтоматический, а при работе с профильными полосами - полностью автоматизирован. В качестве альтернативы подача материала в систему может производиться устройством RotoFeeder® (Engel) или PolyLoad® (Krauss Maffei). Обычно цилиндр и выпуск плунжерного устройства подогреваются до температуры 40 - 50 °C, что облегчает подачу материала.
Обратите внимание!
- Номера партий компонентов А и В силиконового каучука должны совпадать, поскольку согласование системы отверждения производится отдельно для каждой партии.
- Если силиконовая резиновая смесь содержит абразивные вещества, то цилиндры, шнек, стопор обратного потока, игольчатый затвор и литниковые каналы должны иметь твердосплавное покрытие.
RotoFeeder® - зарегистрированный торговый знак фирмы Engel. PolyLoad® - зарегистрированный товарный знак фирмы Krauss Maffei.
ЛИТЬЕ ПОД ДАВЛЕНИЕМ.
ЗАПОЛНЕНИЕ ФОРМЫ И ВУЛКАНИЗАЦИЯ.
Жидкая силиконовая резиновая смесь ELASTOSIL®
В литниковых системах применяются два вида впрыска: непрямой впрыск через холодный канал и горячий вторичный распределитель или прямой впрыск. При этом холодный канал может иметь гидравлический игольчатый затвор. Оба метода впрыска отличаются специфическими преимуществами и недостатками.
Непрямой впрыск
Впрыск материала в гнезда формы производится через холодный канал при помощи литникового распределителя. Завулканизировавшийся литниковый распределитель вместе с изделием необходимо извлечь из формы, отделить от изделия и утилизировать.
Преимущества:
- более дешевое изготовление форм
- подходит для небольших и средних серий
- высокий расход материала (литниковые потери)
- необходимость дополнительной обработки деталей (удаление литникового распределителя)
- не подходит для систем быстрой вулканизации (опасность преждевременной вулканизации в распределительном канале)
Прямой впрыск
При этом методе впрыск материала производится из холодного канала прямо в гнездо формы. Холодный канал с игольчатым затвором обеспечивает дополнительные технологические преимущества, например, незначительный сдвиг материала в процессе впрыска.
Преимущества:
- изделия не требуют дополнительной обработки
- возможность высокого уровня механизации
- незначительный расход материала (отсутствие литниковых потерь)
- возможность работы с системами быстрого отверждения
- высокие затраты на разработку/производство формы
- повышение затрат при использовании многогнездовых форм (необходимость холодного канала для каждого гнезда)
Вулканизация
Температура и время вулканизации зависят от качества системы нагрева, а также материала, объема и геометрии резиновой детали. Как правило, переработка жидкой силиконовой резиновой смеси производится при температуре от 150 до 200 °C.
Сравнение непрямого и прямого впрыска через холодный канал
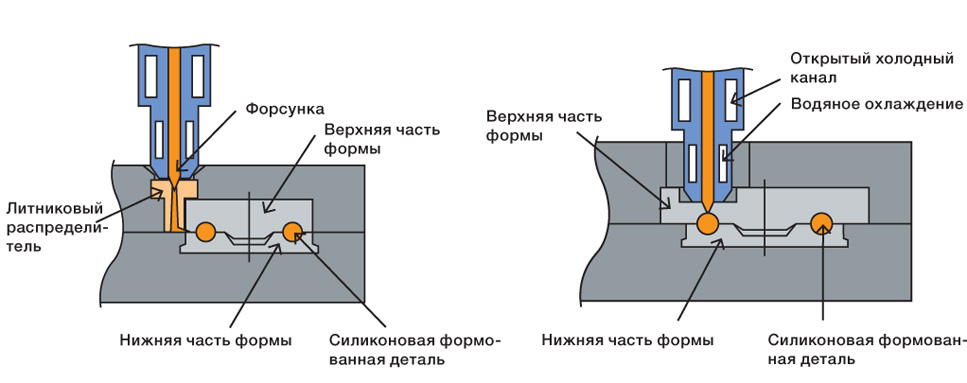
Твердая силиконовая резиновая смесь ELASTOSIL®
Для ее переработки используются практически те же способы, что и для жидкой силиконовой резиновой смеси. Но из-за более высокой вязкости материала сечения литников обычно имеют большие размеры.
Вулканизация
Переработка твердой силиконовой резиновой смеси производится при температуре от 150 до 200 °C.
ЛИТЬЕ ПОД ДАВЛЕНИЕМ.
ИЗВЛЕЧЕНИЕ ИЗ ФОРМЫ.
Вулканизированная силиконовая резина прилипает к стенке формы. Противодействовать этому явлению можно различными способами.
Несколько циклов производственного процесса
Извлечение из формы после первых циклов процесса может сопровождаться определенными трудностями. После нескольких циклов на поверхности форм под воздействием силиконовой резины образуется промежуточный слой, упрощающий процесс извлечения из формы (см. схему).
Смазка
Благодаря использованию смазки, например, ELASTOSIL® формоотделитель 32, процесс извлечения из формы во время первых циклов процесса становится легче.
Вспомогательные средства
Для извлечения формованных деталей из форм обычно применяются штифтовые выталкиватели, щеточные или выдувные устройства.
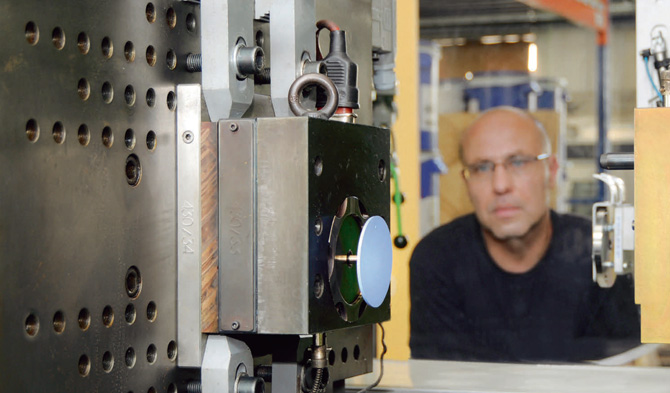
Извлечение отливки из формы
График изменения усилия при извлечении из формы
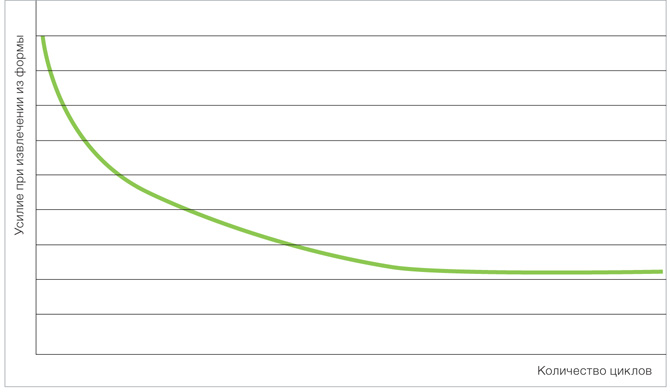