Экструзия
ЭКСТРУЗИЯ
Экструзия представляет собой непрерывный технологический процесс, в ходе которого силиконовая резиновая смесь продавливается через фильеру, а затем подвергается вулканизации. Фильера выполняет функцию формования экструзионного материала. Подающий шнек создает в материале необходимое давление, он также гомогенизирует, уплотняет материал и удаляет из него воздух.
Стандартное применение
Экструзионный метод преимущественно используется при изготовлении таких продуктов:
- шланги
- профили
- кабель
- плоские ленты
- шнуры круглого сечения
Схематическое изображение экструдера с угловой головкой
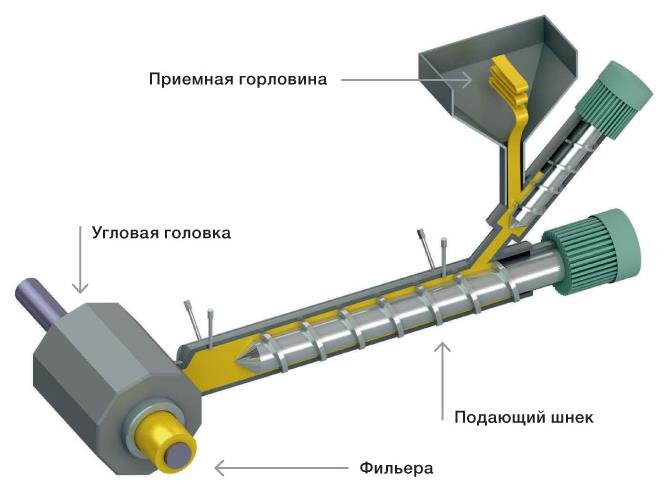
Выбор и подготовка материала
Для экструзии подходит твердая силиконовая резина СИЛФОР®, ELASTOSIL® как пероксидной, так и аддитивной сшивки. Вы можете приобрести материал в виде готовых смесей или же предварительно подготовить компаунд самостоятельно. Для этого резиновая смесь смешивается с необходимыми добавками и сшивающими агентами на вальцах. Чтобы исключить попадание инородных тел компаунд необходимо стрейнировать.
При прохождении через сетку с размером ячеек ок. 100 мкм из материала отсеиваются инородные тела, материал гомогенизируется, и удаляются возможные включения воздуха.
ЭКСТРУЗИЯ
Дозирование
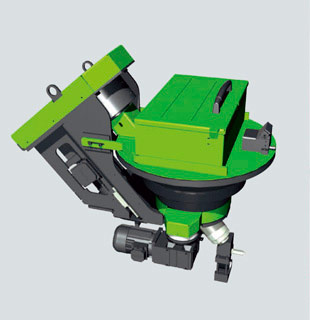
RotoFeeder® - дозирующий узел, используемый при экструзии и литье под давлением
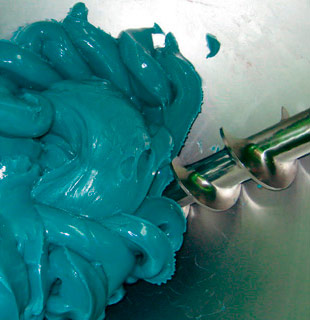
Вид RotoFeeder® изнутри: подающая воронка с подающим шнеком
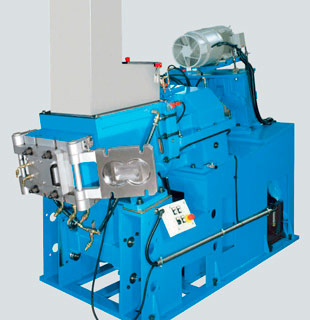
CTM® от Colmec
Подача материала в экструдер должна производиться по возможности равномерно. Процесс подачи может быть ручным, полуавтоматическим или автоматическим.
RotoFeeder® - зарегистрированный торговый знак фирмы Engel. PolyLoad® - зарегистрированный товарный знак фирмы Krauss Maffei. CTM® - зарегистрированный товарный знак фирмы Colmec.
Ручная подача
Для ручной подачи готовится вальцованный лист, который затем разрезается на полоски и вручную подается в приемную горловину.
Полуавтоматическая подача
Для полуавтоматической подачи мы предлагаем специальные формы материала. Полоски каучука сворачиваются в спирали прямо на заводе. Их можно укладывать на вращающееся дисковое намоточное устройство. Управление подачей может интегрироваться непосредственно в систему управления экструдером. Альтернативным вариантом может быть подача спиральных полос прямо из картонных коробок через вытяжное устройство.
Автоматическая подача
Использование дополнительных агрегатов (напр., PolyLoad® от Krauss Maffei, RotoFeeder® от Engel или системы CTM® от Colmec) автоматизирует процесс подачи и дозирования. Материал подается в накопитель, в котором вращается один или несколько шнеков. Через выходное отверстие шнек непрерывно подает материал в экструдер. При этом можно использовать любые поставляемые формы твердой силиконовой резиновой смеси ELASTOSIL®/Silpuran®/SilFor®.
ЭКСТРУЗИЯ
Подача материала
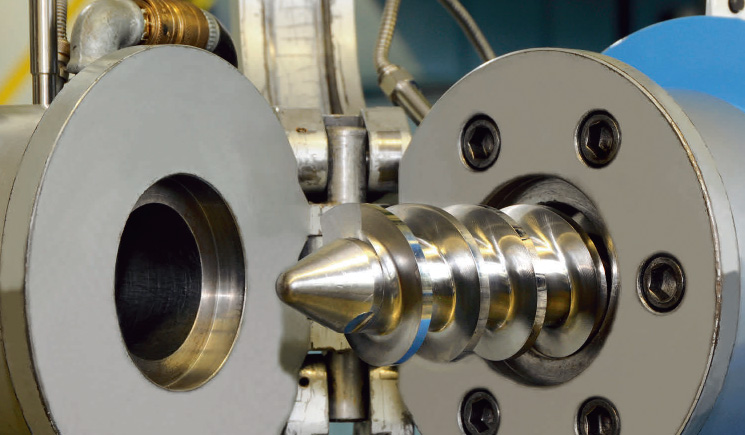
Открытый экструдер с подающим шнеком
Шнек выполняет в технологическом процессе насколько функций: он транспортирует и уплотняет смесь, а также создает давление материала и одновременно удаляет из него воздух. Управление гомогенизацией, обратным удалением воздуха и давлением продавливания материала производится путем изменения геометрии шнека и параметров машины.
Конструкция шнека
- Чтобы упростить захват материала, расстояние между заходами шнека в зоне захвата должно быть максимально большим. Свою эффективность также доказали углубления в зоне захвата.
- Для использования подходят одно- или двухзаходные шнеки со степенью сжатия от 1 : 1,5 до 1 : 2. Пропускная способность двухзаходных шнеков выше.
- Предпочтительнее использовать шнеки с увеличением диаметра или шага витка. Диаметр увеличивается от зоны захвата к зоне разгрузки. При увеличении шага витка расстояние между витками в направлении от зоны захвата к зоне разгрузки уменьшается.
- Стандартное соотношение длины шнека к его диаметру равно от 10 : 1 до 12 : 1.
- Чтобы предотвратить преждевременную подвулканизацию материала сам шнек и кожух цилиндра необходимо охлаждать.
ЭКСТРУЗИЯ
Экструзионная оснастка
Формование вулканизата выполняется при помощи зкструзионной оснастки (фильера). Конструкция фильеры такова, что силиконовая резиновая смесь не требует каких-либо специальных операций, ее качество определяется стандартными нормативными документами.
- Толщина стенки фильеры должна быть одинаковой на всех участках.
- Избегайте сходящихся под острым углом граней и углов - они могут стать причиной шероховатых поверхностей экструдата.
- Следите, чтобы по ходу движения потока не было мертвых зон и резких изменений направления - в углах может происходить скопление и подвулканизация материала.
- Важным фактором является равномерная скорость потока по всему сечению. Скорость потока материала снижается прямо пропорционально удалению от центра фильеры. Поэтому для получения изделия с прямыми гранями грани фильеры должны быть вогнутыми.
Выравнивание вздутий
На выходе экструдата из фильеры возникает вздутие. Появление вздутия определяется следующими факторами:
- вязкостью (снижение вязкости ведет к увеличению вздутия)
- температурой (повышение температуры ведет к увеличению вздутия)
- скоростью экструзии (повышение скорости ведет к увеличению вздутия)
- диаметром фильеры (уменьшение диаметра ведет к увеличению вздутия) Если скорость транспортера нагревательного канала превышает скорость выхода экструдата из выходной фильеры, то возможна так называемая вытяжка экструдата. Тем самым можно установить необходимый диаметр экструдата. Это позволяет компенсировать вздутие и производить вулканизаты, диаметр которых меньше отверстия фильеры.
Изменение геометрии фильеры
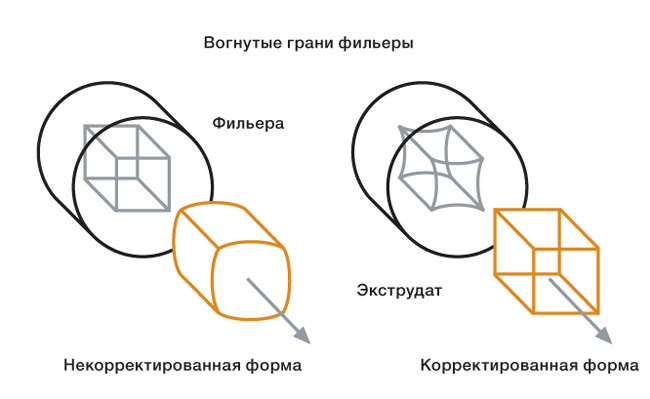
Изменение граней фильеры для открытого профиля
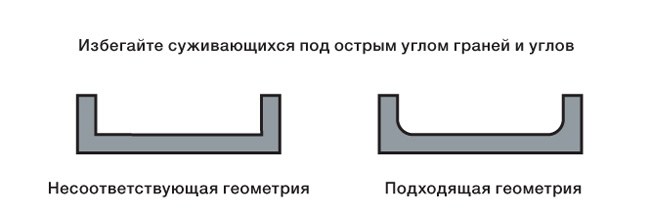
ЭКСТРУЗИЯ
Вулканизация
Как правило, вулканизация экструдата производится в вертикальных или горизонтальных линиях нагрева, под избыточным давлением или без избыточного давления. Вулканизация силиконовых каучуков в соляной ванне используется редко, но в принципе ее можно применять для смесей пероксидной вулканизации.
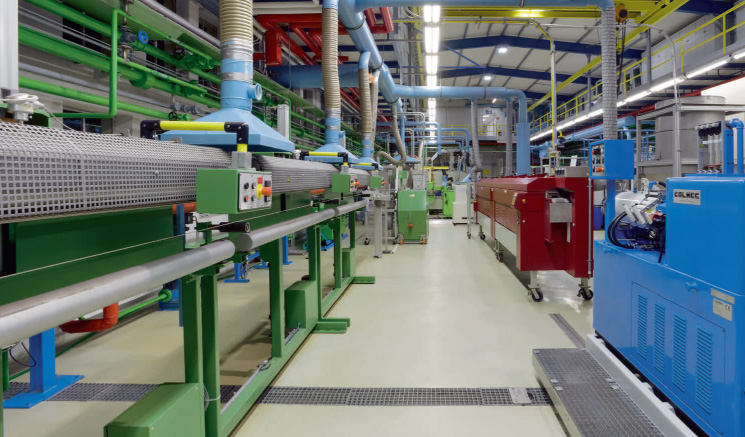
Производство кабеля: экструзия с последующей вулканизацией в инфракрасном канале
Вулканизация в линиях нагрева без избыточного давления
В процессе производства шлангов и профилей чаще всего вулканизация производится в линии нагрева (при температуре от 200 до 500 °C) без избыточного давления. Нагрев в вертикальных или горизонтальных каналах осуществляется при помощи инфракрасных стержневых нагревателей с рефлекторами, установок подачи горячего воздуха или керамических «темных» инфракрасных излучателей.
Транспортировка экструдатов осуществляется транспортерными лентами из стального листа или стальной сетки. Транспортерные ленты перемещаются на подвижных концевых роликах, что позволяет компенсировать тепловое расширение ленты. Скорость движения ленты можно регулировать. Для предотвращения чрезмерного охлаждения обратный ход транспортерной ленты также выполняется в нагревательном канале. Если это невозможно, то быстрое остывание можно предотвратить специальными укрытиями.
Чтобы предотвратить появление отпечатков транспортерной ленты в горизонтальныхт линиях нагрева возможна предустановка шок-канала, в котором будет происходить предварительная вулканизация при температуре ок. 600 °C. В большинстве случаев предпочтительнее использовать вертикальную экструзию при помощи угловой экструзионной головки. Это поможет предотвратить появление отпечатков транспортерной ленты, при этом появляется возможность обработки очень мягких материалов.
Вулканизация в линиях нагрева с избыточным давлением
Вулканизация при помощи установок с паровой камерой используется прежде всего для производства кабелей. Теплоносителем в таких установках является находящийся под давлением пар. Как правило, пар подается в установку под давлением от 4 до 20 бар. Для достижения температуры вулканизации необходимо давление не менее 6 бар. Температура пара определяется давлением подачи.
При этом методе на экструзионную головку постоянно подается насыщенный пар. Поэтому для предотвращения подвулканизации экструзионная головка должна интенсивно охлаждаться. Время вулканизации зависит от длины линии, температуры и толщины стенок изоляции. Обычно оно составляет от 0,5 до 2 минут.
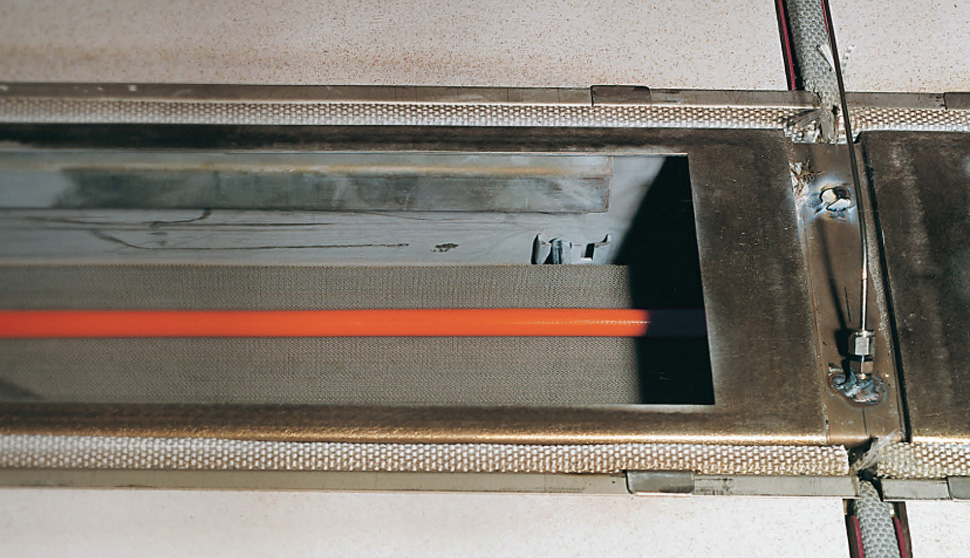
Вулканизация трубки в горизонтальном канале горячего воздуха
Общие указания по экструзии
Охлаждение
Вследствие сжатия - неотъемлемой составляющей экструзионного процесса - сдвиг материала происходит с высокой скоростью, что ведет к выделению тепла.
- Поэтому для предотвращения подвулканизации необходимо охлаждение. Интенсивность охлаждения должна обеспечить температуру резиновой смеси намного ниже точки распада пероксида или точки начала активности платинового катализатора.
- Максимальная пропускная способность цилиндра возможна при охлаждении.
Габариты экструдера
- Хорошо показали себя экструдеры с диаметром шнека от 45 до 90 мм и соотношением длины шнека к его диаметру от 10 : 1 до 16 :(стандарт - от 10 : 1 до 12 : 1).
- Чем больше габариты экструдера и шнека, тем меньше число оборотов и количество фрикционного тепла.
Коэкструзия
Метод коэкструзии дает возможность получать экструдаты из разных материалов. Так производятся шланги с полосой, окрашенные экструдаты или полосы с дополнительно экструдированным профилем. Для данного метода WACKER предлагает самоклеящиеся типы силиконовых резиновых смесей ELASTOSIL® R плюс.
ЭКСТРУЗИЯ
Устранение дефектов
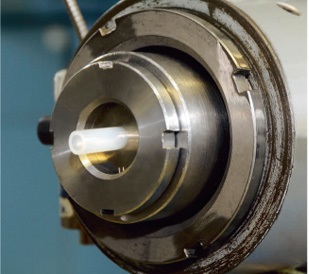
.jpg)
В представленной таблице указаны самые частые дефекты материала и возможные причины из возникновения. Если у вас появились дополнительные вопросы, обратитесь к эксперту компании Евро Кемикалс.
Общие рекомендации по предотвращению дефектов
- В результате смешения материал должен стать однородным, без загрязнений.
- После каждого производственного процесса необходима тщательная очистка экструдера.
- Не допускайте колебаний температуры и давления материала.
- Следите за равномерностью подачи материала в экструдер.
- Используйте специальные сетки (удаление воздуха из материала, предотвращение колебаний давления)
- Регулярно проводите техобслуживание всех машин и механизмов.
Дефект |
Возможная причина |
---|---|
Пузырьки |
Наличие в машинах влаги, включения воздуха |
Загрязнения |
Отсутствие сетки, подвулканизация отдельных частиц вследствие слишком высокой температуры материала, неоднородность смеси |
Хрупкость экструдата, белые полосы при вытяжке экструдата |
Появление дефектов материала из-за слишком высокой температуры отверждения. |
Мягкая зона круглой формы в центре экструдата |
Недостаточная вулканизация, слишком большая скорость линии или слишком низкая температура |
Сходящиеся под острым углом грани экструдата имеют «зубчатую» форму |
Неправильная конструкция фильеры |
Непостоянство геометрии экструдатов |
Колебания давления или температуры материала |
Шероховатая поверхность |
Наличие царапин/повреждений на поверхности фильеры, слишком высокая температура материала |